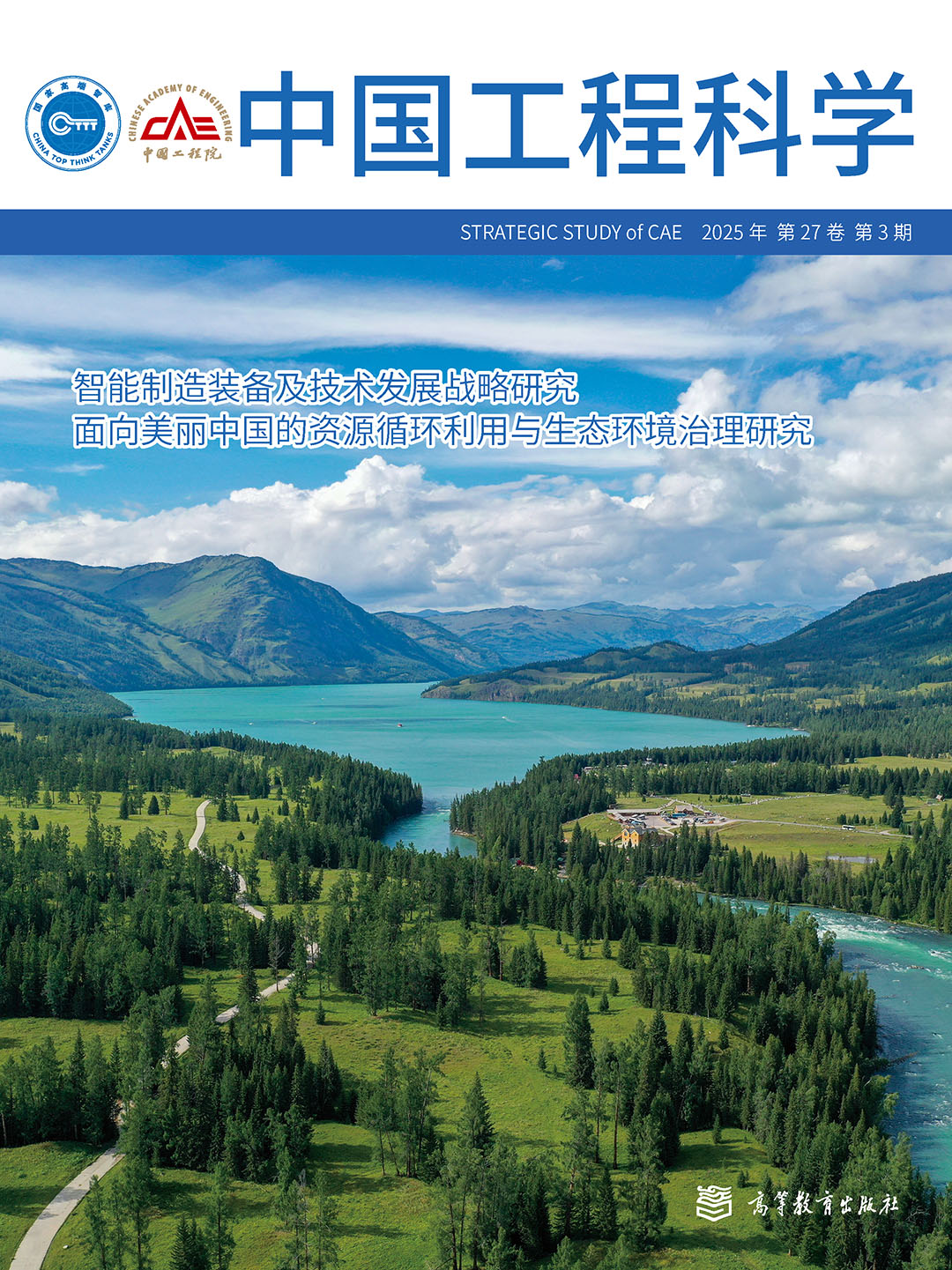
一、 前言
高端制造业是我国重点培育和发展的新兴产业,在支撑国家重大战略、引领国民经济发展、维护国家安全方面具有重要价值。航空航天、轨道交通、海洋船舶、工程机械等重大装备的制造水平代表了一个国家的工程科技核心能力,成为工业强国竞争的制高点。我国高端制造业经历了近20年的快速发展,涌现出一批标志性的重大装备,但在“空 – 地 – 海”探索持续深入且对装备性能要求进一步提升、国际竞争愈发激烈的背景下依然面临迫切挑战[1~3]。
智能制造系统指具有自主感知、高效决策规划、精准执行等功能的制造系统,是高端制造业的重点发展方向,工业机器人则是智能制造系统最主要的构成要素。新一轮工业革命加速到来,发展智能制造和工业机器人成为工业大国的战略部署。美国发布“国家机器人计划2.0”“机器人发展路线图”“无尽前沿法案”等,将智能机器人、先进工业制造技术列为发展重点;欧盟提出“火花计划”“地平线2020计划”等,着力增强机器人的高柔性自主作业能力。我国也提出,以新一代信息技术与制造业深度融合为主线,重点发展机器人与先进制造产业,全面提升中国制造的质量和智能化水平[4,5]。
当前,智能制造工业机器人技术发展迅速,在制造领域的磨抛、移载、检测、装配等关键工序中逐步获得应用。然而,机器人作业的感知、规划、控制策略等仍显单一,仅能执行简单和重复的任务,缺乏对制造场景的深入理解、“机器人 – 设备 – 环境”复杂智能交互的能力;大量的制造任务依赖人工,智能化、柔性制造亟待增强。合理预判,工业机器人作业将进一步发展,越来越多地应用于智能制造任务,也将成为航空航天、轨道交通、海洋船舶、工程机械等重大装备核心零部件加工制造的主要形式。
面向上述重大背景与技术演进方向,本文围绕智能制造工业机器人的基础理论与关键技术,梳理应用现状、辨析研究进展、凝练发展趋势,为深化工业机器人技术研究、推进我国智能制造发展、论证新兴产业高质量发展等提供基础参考。
二、 智能制造工业机器人应用现状
(一) 工业机器人应用背景
在全球制造业高速发展的背景下,机械工程、人工智能(AI)、电子信息等技术的快速发展提高了机器人的智能化水平,以工业机器人作业系统为代表的智能制造技术成为国内外制造业的关注焦点。智能制造工业机器人具有作业灵活、自适应性强的特点,基本型包括作业执行机构、机械臂两部分;也有在此基础上增加移动底盘构成的复合机器人(见图1),进一步增强机器人的作业适应能力。以航空航天、轨道交通、海洋船舶为代表的高端制造领域,在核心零部件的检测、加工、装配等制造工序中逐步引入了智能制造工业机器人技术。
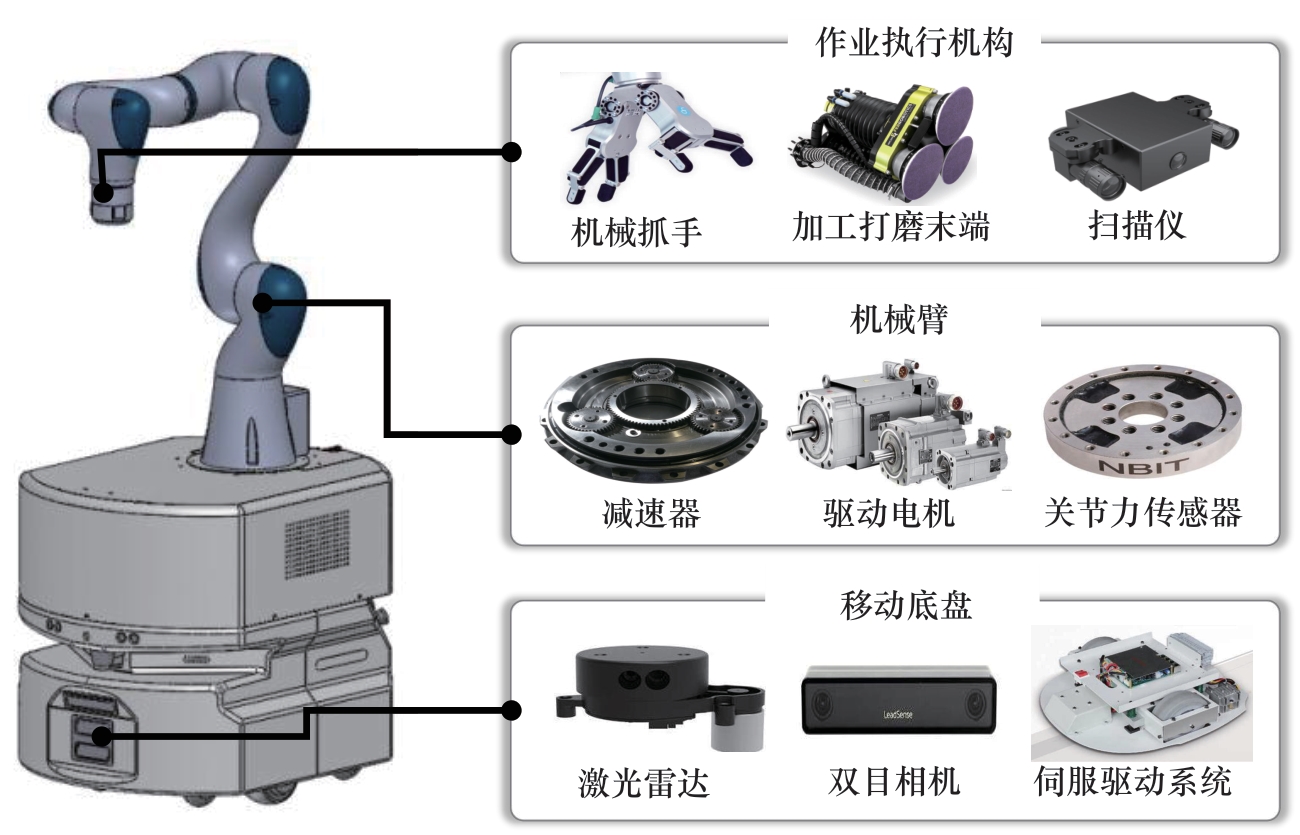
图1 智能制造工业机器人的主要构成
目前,工业机器人聚焦于制造过程中的单一功能或单一工序,因缺少协作机制而仅能执行简单任务;在环境理解、状态感知、多任务规划、协同柔顺控制等方面开展了较多研究并取得一定进展,但整体技术水平未能达到自主解决“机器人 – 设备 – 人 – 件”复杂环境交互问题的层次。工程化的智能制造能力有所不足,智能制造的体系支持能力也显缺乏。
工业市场需求快速变化、制造技术快速迭代,小批量、多品种、柔性化、易部署的多机器人智能制造系统将成为发展主流,驱动多机交互、人机交互、机器人与场景交互的广度和深度不断提高。针对这种复杂交互的需求,围绕动态场景理解、集群化作业、具身智能、场景网络化、灵巧柔性作业、数字孪生等方向,逐步构建感知 – 规划 – 控制一体化的智能制造工业机器人复杂多维协同作业机制,推进制造模式柔性化、制造过程信息化、制造工序无人化的新型生产方式。由此,为高端装备制造难题提供新型解决方案,促进工业制造的数字化、网络化、智能化转型升级。
(二) 工业机器人作业类型
1. 智能视觉检测
检测对象多变复杂,针对性开展精准实时的缺陷检测是复杂零部件制造的难题之一。在二维图像检测方面,通常在机器人末端安装相机,再通过机器人“手眼”协同的方式开展工件表面检测[6]。智能相机逐步投入应用[7],基于深度学习方法构建面向外观缺陷的检测架构,以相机、处理器、视觉软件集成优化的方式提高了图像检测速率。在精密电子、机械耗材制造等行业,多采用搭载多光谱拍摄、图纹投影照明技术的视觉检测系统[8]开展工件外观缺陷检测。在三维视觉检测方面,传统的三坐标测量、激光测量逐步升级为不接触部件表面的光学测量方法。对于大尺寸部件测量,建立了“扫描仪+机器人”的复合测量平台,提高了三维测量系统的柔性和灵活性。这些三维测量系统采用机器人、固定转台配合的测量视角变换方式,可在一定限度内完成部件的三维测量。在测量框架方面,多基于几何特征来确认测量点[9~11]。金属零件抛光面或漆面检测具有弱纹理的特点,可采用无分支散度的复杂零部件缺陷检测、六自由度姿态估计方法[12]进行多表面检测。
也要注意到,现有的二维 / 三维检测方法在中近距离检测测量时效果较好,而对于大尺寸、稀疏特征的表面以及多层交织的复杂结构表面而言,检测效果不尽如人意;检测机器人缺乏场景环境感知能力,难以在人、物料、设备共存的复杂检测场景下进行测量扫描作业。
2. 高效磨抛
机器人高效磨抛是智能制造工业机器人技术最具有代表性的应用场景。机器人关节多、自由度高,在末端控制、运动算法的支持下可执行灵活作业,接近人类的作业形态。在人机协作配合、机器人运动及工序设置合理的情况下,机器人磨抛系统能够长时间地连续作业并保持系统稳定。控制程序可驱动机器人按照预设的轨迹执行高精度的重复动作,获得的产品一致性优良。在设备运行状态良好、安全保障措施到位的情况下,机器人磨抛作业可以减少甚至无需人工参与(人仅在外围进行远程监控和紧急操作),实质性降低作业的危险性[13]。
机器人高效磨抛受到制造业的广泛关注,磨抛机器人的研制及应用成为热点。主流的机器人磨抛系统一般采用恒力控制模式,机器人打磨末端沿固定轨迹行进[14],适应多种工件的毛刺、端面、金属堆附等打磨场景。在使用普通的六维力传感器以外,也有基于气控浮动打磨机器人末端执行器来提高磨抛末端力控制精度的做法[15]。除了通用型号,还针对航空航天、海洋船舶等行业的特定需求,研制了专用型磨抛机器人系统。例如,航空领域的叶片机器人磨抛系统搭载了六维力传感器,适用于涡轮叶片铸件粗磨、机加叶片精磨、成品叶片抛光的一体化加工[16];发动机缸体自动化砂带磨抛设备也属此类[17]。
机器人磨抛技术发展时间较长,但受限于机器人弱刚性以及臂展空间不足,开展全表面打磨仍然极为困难;任务执行的灵活性、柔性有待增强,如选择磨抛路径依赖人工经验,缺乏高效规划方法。
3. 柔性精密装配
工业制造场景多样,从大尺寸的航空航天装备部件制造到微尺寸的电子元器件,均广泛涉及装配工序。主流的机器人装配研究、自动化生产线应用多涉及轴孔装配,根据轴孔匹配数量细分为多轴孔装配、单轴孔装配[18,19],具有装配动作单一且装配间隙较大的特点。随着装配场景中零部件接触面形貌的复杂化,装配难度不断增加,装配间隙也因装配场景要求不同而显差异化;对于一些精密装配场景,装配间隙将直接降低装配精度[20,21]。实际装配过程多存在非标准、不规则的异形零部件,进一步加大了机器人装配的难度。
结合目标装配工件的表面及轮廓特征,通过视觉、接触力传感进行复杂异形零部件的移动、装配对准、位姿调整,由此实现自动化装配工序[22,23],如发动机、电机、变速箱等部件的轴孔装配、榫槽装配等,是目前广泛应用的方案。为进一步提高装配进度,对于零件和标记量具的插拔,也可采用根据装配空间的几何约束特性求解机器人控制器柔顺轨迹跟踪的力和力矩参考值的方式[24,25]。针对零部件装配面挤压的微形变问题,建立了装配的弹性接触机理分析模型[26],近似计算出输入力/扭矩、反作用力/扭矩、接触压力、接触形变等参数的变化关系。采用连杆运动模型[27]、三点接触模型[28]等特定模型来描述装配接触系统,在过盈配合联接、胶接、压圈等复杂力交互的情况下应用较多。
整体来看,当前的机器人只能完成相对简单的装配任务,且以单个机器人的装配为主;机器人协同作业能力不佳,难以应对复杂力交互、多零部件的装配过程;机器人的灵活性不足,不适用配合组件的复杂长程装配。
4. 工件抓取转运
在高端制造场景中,待加工的工件摆放随机,空间障碍复杂,待抓取工件的位置及姿态不尽相同。需要机器人根据每次视觉系统的测量结果重新规划运动轨迹,同步保证运动路径不会与其他作业设备、现场工人等障碍碰撞。工件抓取转运作业对机器人的动态路径规划、避障能力等提出了较高的要求。需要创建运动规划的环境模型(含机器人、待抓取的工件、作业环境中的障碍物等),支持开展机器人的抓取运动、移动路径等规划。
避障检测同样基于点云数据处理算法,涉及工件的计算机辅助设计(CAD)模型、机器人末端抓手的简化CAD模型。通常参考避障策略设计机器人的抓取方法[29],据此选择抓取点;针对机器人、抓取点的运动轨迹进行滤波器平滑,形成最终的机器人运动轨迹指令,发送给机器人控制系统。机器人抓取搬运作业已有成熟方案[30~33],如机器人视觉抓取系统。抓取系统一般采用固定安装方式,也可布置在机器人末端;设计了多种工具单元,配合基于模型匹配的零部件定位算法,支持机器人对无序堆叠零部件进行抓取转运;集成了工件跟踪定位、位姿估计、避障规划等功能,在车架、电机、盖板等制造场景中获得应用。例如,在汽车零件制造流程中,采用机器人进行三维视觉定位与抓取作业,从包装箱抓取多层摆放的零件;基于点云数据、零件的CAD模型,进行曲面的表面法线向量估计、曲面分割、几何建模、目标物体的识别及位姿估计;将获得的工件位姿信息发送给机器人控制系统,引导机器人运动并抓取工件。
值得指出的是,主流的机器人抓取搬运方法多基于模型信息,较少引入待抓取零部件搬运过程中因机器人之间相对位置偏差而产生的物体形变,导致抓取搬运物品形状损坏或应力难以释放。设计机器人灵活抓取机构,可在一定程度上缓解相关问题。
(三) 工业机器人制造场景
1. 航空航天装备制造
相较传统制造行业,航空航天装备制造具有空间尺寸大、加工材料特殊、机械结构复杂、性能指标要求高的特点,对加工、装配作业机器人的灵活性、安全性、可靠性、稳定性等都提出了更高的要求。工业机器人广泛应用于飞机零部件的加工和装配,可提高制造自动化程度、降低制造成本、合理缩短交货时间[34]。在飞机总装流程中,由钻孔、检测等功能的机器人组成的多机器人协同装配系统[35],提高了机身段对接装配30%的作业效率;针对壁板、蒙皮、长桁等柔性复合材料部件,采用多机器人配合完成抓取、转移、放置等任务[36]。包含测量机器人、钢绞线定位机器人、夹装配机器人、机身钻铆机器人等复杂多机器人在内的飞机自动总装系统已进入技术验证阶段[37]。在内机舱组装流程方面,由机器人执行装配中交叉孔的镗销工艺[38],可保证镗孔质量和位置精度,在飞机装配项目中获得应用。引入小空间仿生机器人开展内仓支架、角片的组装操作,构建了空中客车A350机身前段的内部支架[39]。在飞机装配检测环节构建了机器人应用程序,如采用红外相机、激光雷达、深度相机获取检测区域三维数据的测量方案[40]。
2. 海洋船舶制造
我国造船企业占据一定比例的全球市场份额,但制造环境不佳、劳动强度大、作业效率低、加工误差不稳定等问题制约着船舶制造行业的高质量发展。机器人制造技术在造船企业的推广应用,推动造船生产制造流程的优化,提升造船效率并保障制造质量,如成功应用于切割、焊接、涂装、装配、搬运、检查、清污等船舶制造任务场景。船舶涂装工艺是船舶制造的支柱工艺之一(成本占总船价的8%~10%),目前仍以人工作业为主;由自动导向车、升降机、机械臂、喷涂模块等构成的移动喷涂系统正在研发过程中,后续将应用于船舶的大型非结构外壳体表面的自动涂装[41,42],可显著压缩工艺成本并提高制造效率。焊接是船舶制造另一个主要工序,约占全部建造施工量的1/3,焊接水平成为评价造船质量的重要指标。针对船舶焊接一致性、精度等方面的问题,基于视觉引导机器人进行焊接和检测作业[43,44]为研究热点,目标是提高焊接的鲁棒性、准确性,着重增强非连续焊缝的主动识别、跟踪定位、精准焊接能力。此外,自动化船体检测也是关注重点,包含船舶整体合拢口、模块测量和船体/船舱焊缝、漆面等的检测;采用升降机构配合机器人或磁吸附攀爬机器人的作业方案[45,46],可有效减小船舶测量中机器人检测结果的偏差,全面改进船舶的检测流程。
3. 轨道交通装备制造
轨道交通是国民经济发展的重要保障,在综合交通体系中占据骨干地位[47]。轨道交通装备制造是现代综合交通运输、现代化制造产业体系建设的重要内容,在装备制造业发展中肩负重要使命。白车身是高速列车的大型复杂部件,车身制造的核心工艺是焊接和打磨,相应质量关联高速列车的运行性能与安全;但白车身打磨仍以人工作业为主,效率低且工作环境不佳,因而基于机器人的自动化打磨能力[48]成为亟需。在动车转向架、机车司机室的焊缝打磨中开展了研究和测试性应用,对于大、长、直焊缝,小弧形焊缝,机器人能够灵活切换不同的打磨工具并执行作业,也可通过传感器对工件、打磨工具的偏移量进行精准计算与自动补偿,兼顾打磨质量和校准速度。此外,在轨道交通大型复杂部件的装配过程中,国内企业采用多机器人协同作业,实现了列车车身的自动化搬运、转向架侧梁内腔等结构的自动化组装[49]。
4. 新能源汽车制造
新能源汽车市场快速增长,成为汽车工业的重要发展方向。新能源汽车制造工序多、产线节拍快,对大容量、多设备、高效协同的智能制造能力提出了极高要求。在汽车车身制造方面,发展了视觉、力觉等传感引导的多机器人协同车身制造工作站,构建了包含多异构机器人、多传感设备、变位机与夹具、机器人桁架以及排尘等配套辅助模块在内的车身定位/焊接/搬运系统;采用顺序功能图分析焊接工序,据此规划控制系统的通信架构,与企业研发管理系统连接,支持汽车部件多机协同制造[50,51]。在动力电池的安装与搬运环节,更多采用基于工业机器人的自动换电方案,模拟人工换电的过程并由机器人进行电池抓取(结合堆垛机进行电池存放),实现动力电池装卸、在汽车和电池仓库之间的搬运[52,53]。
5. 电子信息产品制造
电子信息产品指计算机类、通信类、消费类电子产品,相应制造在工业体系中占据了重要份额。电子零部件尺寸较小、元件标准化程度较高、产业智能化整体进展良好,工业机器人在相关制造中获得广泛应用,主要执行检测和装配作业[54]。在电子零部件的转运和安装方面,多采用由机器人、视觉传感器(通常为工业相机、激光扫描设备)构成的机器人作业系统,对零部件摆放进行精确定位、姿态估计以及执行抓取和安装工序[55,56]。针对零部件板型、螺孔、定位孔、卡扣等结构的机器人在线视觉检测系统,通常在数秒内即可完成单个工件的多项表面参数光学检测[57]。机器人视觉检测分拣具有高速、稳定、智能、易部署的特点,适用于批量尺寸检查与自动装配、产品完整性检查、元件定位、表面字符识别、印刷电路板检验、元器件引脚定位等电子制造场景。
三、 智能制造工业机器人共性技术研究进展
得益于庞大的制造业需求,智能制造工业机器人技术应用面极为宽阔,也获得了系统性的发展,但在复杂制造场景理解、主动灵活作业交互等方面仍有明显不足。解决之道是从视觉感知、决策规划、运动控制、灵巧机构设计等方面开展工业机器人的共性技术研究。
(一) 视觉感知
1. 环境理解与状态感知
工业制造场景范围较大,人、机器人、设备、物料同时大量存在并不断移动变化。这种动态变化的大范围制造场景对机器人的实时环境理解与状态感知能力提出了极高要求,需要机器人在自主感知和理解当前环境的基础上构建环境地图、感知作业状态。机器人语义地图构建方法主要有基于视觉的同步定位与地图构建(SLAM)、基于激光的SLAM、多传感器融合等。视觉和激光SLAM方法通过最小化距离估计位姿,重建效果较好且计算量小,得到广泛应用[58~61]。然而相关算法在面对更高级语义要求的场景时有所不足,将语义理解和环境构建相结合则可改善机器人对复杂作业环境的理解能力,如引入语义信息实现复杂室外场景中的多类型分割识别,建立基于语义理解的长期语义地图维护机制[62,63]。为提高应用的实时性,结合拓扑先验知识、编码 – 解码器深度网络开发了环境语义理解方法[64],引入先验知识以加速语义理解过程,在避免依赖标注的同时提高了语义分割识别的精度。需要指出的是,目前的环境理解局限在室内、室外、自动驾驶等场景(语义分割精度无需精确到毫米级、环境要素种类偏少),难以满足重大装备制造场景的多要素、高精度、高维细粒度等要求。
机器人状态感知的信息有位姿、变形等影响工件质量关键表面参数的信息,裂纹、凹坑等表面缺陷信息。在机器人运行轨迹监测方面,建立不同轨迹、初始位置、运行参数、图像中作业位置 / 轮廓之间的映射关系,再基于卷积神经网络进行机器人运行轨迹的跟踪即监测[65]。在目标位姿估计方面,相关研究集中在基于目标边缘、关键结构注意力机制的位姿估计策略[66],较好解决了光照多变、无纹理物体条件下的姿态估计问题。在作业过程形变感知监测方面,分析毛坯的成形误差、切削力与内应力变形等因素,重建考虑阻尼效应、外部载荷的动态位移和应变场,据此监控机器人作业过程中的外形几何形变、实施机器人运行补偿[67,68],保证成品精度。然而,重大装备制造过程工艺复杂、工序繁多、场景多变,需要综合且实时地感知多种状态,现有的感知方法仅适用单一模态制造状态,难以满足相关场景中集群机器人的自主作业需求。
2. 全尺寸三维检测
三维检测指扫描数据与设计模型数据的三维误差计算过程,实质是比对三维扫描数据与工件模型数据的匹配及偏差情况,获得目标表面的三维误差分布,在打磨、抛光、机加工、焊接等环节得到广泛应用[69,70]。在三维检测后,机器人加工系统根据测量结果调整零部件的加工参数,优化抛光、打磨等后续工序。全尺寸三维检测主要针对大尺寸部件、表面结构复杂的部件,在扫描视点规划、尺寸测量的基础上精确计算部件的外形及结构尺寸。扫描视点规划旨在确定最佳成像视点,引导扫描仪完成目标的三维扫描任务;通常采用体素、三角网格等模型描述扫描空间,推算遮挡区域后确定扫描视点[71~74]。
尺寸测量指基于模型的几何特征进行数据匹配(如体素截断符号距离或欧几里得符号距离信息),或者根据测量的工艺特点构建测量评价函数[75],由平方最小化[76]、方差最小化[77]原理求解,可综合运用多种方法来进一步提高测量精度[78]。应用特征和几何信息的匹配策略(如关键点搜索、几何约束设置、数据点权值分配),也可提高零部件扫描数据配准算法的收敛速度及鲁棒性。根据测量余量分布要求确定误差函数后,设计模型数据、三维扫描数据的配准测量过程可视为求解非线性的多维优化问题。当然,三维测量方法易受原始三维扫描数据中的背景数据噪声、数据匹配次序的影响,导致配准结果产生偏移进而降低三维检测结果的准确性。
(二) 决策规划
1. 机器人多任务调度
对于复杂任务场景,单个机器人通常无法满足制造任务需求,因而需要多机器人协作。机器人多任务调度涉及任务工序的执行顺序(任务工序调度)、每个任务的承担机器人(任务分配),较多采用启发式搜索策略,即由运行过程中的环境信息启发机器人系统的新搜索方向,获得任务调度优化问题的近似最优解(见图2)。代表性的研究有利用蚁群启发算法探究协作机器人的任务分配问题[79]、基于启发式算法解决静态时间扩展的多机器人任务分配问题[80]、引入大邻域搜索策略优化多机器人/多工序任务的调度与分配问题[81],相关方法初步应用于工程机械、飞机机身等结构件的制造过程。相比精确求解类方法,启发式方法只寻求近似最优解,搜索效率较高,适合计算规模较大的场景,但带有难以调整的超参数,明显影响求解质量,不适合处理动态任务。
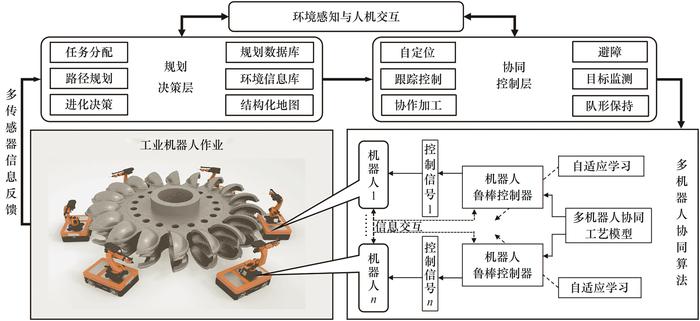
图2 基于环境感知的智能协同规划控制系统
不同于启发式方法,市场机制类方法采用分散式的控制方式,适合大规模动态分布式系统,具有良好的可扩展性和鲁棒性,在高动态环境中的任务调度分配方面效果更好[82,83]。为应对机器人任务执行期间的意外及不确定场景,可将单一市场交易策略扩展为动态权重的拍卖策略[84],支持多机器人作业系统中时间约束任务的预先分配与动态分配。市场机制类方法的搜索过程通常采用贪心式决策,计算简单但很难获得全局最优解。
目前,机器人多任务规划开始探索应用强化学习方法,基于Distributed-Q算法的强化学习模型[85]、基于分层强化学习的多任务梯度规划[86]、深度强化学习规划[87]等较好解决了大规模复杂环境下多机器人协同作业任务调度问题。类似强化学习方法,模仿学习[88]也可应用于多机器人作业状态预测,支持多机器人安全路径规划。强化学习、模仿学习将学习到的策略函数直接映射成目标决策,相较传统的搜索方法具有更高的计算效率和实时性;但在求解问题规模较大时会出现状态空间“爆炸”情况,导致学习过程不易收敛。
2. 复杂场景无干涉协同规划
机器人末端一致性作业规划是复杂的多约束高维规划问题。面向复杂部件制造场景,机器人系统作业端的运动规划还需满足空间狭小、动态分析、实时避障等需求。机器人作业端协同系统主要包括主从式、分布式两种。
主从式系统选择1个机器人作为主机器人,其余的定义为从机器人。根据主从机器人之间的协调关系与目标位置,规划主机器人的运动轨迹,再根据主机器人的轨迹进行从机器人的运动轨迹规划。例如,在基于任务分类的机器人规划策略中,通常对不可行任务与机器人分配进行编码[89],并对未来可能出现的类似分配进行剪枝处理,生成可执行任务的机器人运动规划约束,形成机器人复杂任务规划。为应对避障问题,多采用机器人作业运动虚拟区域的策略[90],改变虚拟区域移动方向及矩形参数以适应作业环境,在考虑虚拟区域参数变化的同时及时调整机器人的移动方向。主从式系统的结构整体性、协调性较好,但集群机器人的运动轨迹存在耦合概率,成员的误差及故障会被放大,不利于整个系统的稳定性和可扩展性。
在分布式规划的框架下,机器人根据自身传感器的信息规划自有运动,机器人之间以通信方式交换各自的位置和环境信息。典型的分布式规划策略是基于速度障碍(VO)的方法[91]。VO起初用于处理动态环境下机器人的运动规划问题,将避障问题转化为速度调整问题;将预测碰撞的速度区域定义为VO区域,选择VO区域之外的速度作为避障速度;当场景中的机器人数量较多时,会出现避障引起的抖动现象。为此提出了交互速度障碍算法[92],为机器人提供统一的行为决策与规划并避免抖动现象,但在机器人规模进一步增大后仍然难以避免碰撞。此外,分布式规划方法虽然适合动态环境场景,但大量的分布式通信交互对通信带宽要求较高。为了高效表征多机器人任务规划系统、增强多机器人任务规划能力,有研究将之视为构型空间维度更高的单机器人系统,探索了基于策略梯度模型的机器人运动规划策略,在复杂动态环境中单移动机器人的实时运动规划与调度、多机器人协作动态环境中机器人单元的运动规划[93,94]等方面展现出良好潜力。
(三) 运动控制
1. 多机器人协同控制
机器人尤其适用多型号、小批量的大型构件加工,而复杂的机械连接结构致使末端刚度较低,进而导致加工精度普遍不高。机器人控制优化的重要研究方向即为基于接触力模型预测和补偿的机器人刚度增强方法,用于改善加工质量及稳定性[95]。通行的做法是建立打磨、抛光、切割、去毛刺等任务的机器人运动学、动力学、刚度模型,据此优化机器人的位姿/接触力分布,提高加工精度。以机器人铣削加工为例,根据运动学、动力学模型来优化位姿、提高刚度,建立机器人铣削模型并分析铣削参数和工艺流程,增强机器人铣削颤动抑制能力。结合传感器反馈的六维铣削力信息,计算机器人的端偏移,通过算法对轨迹进行补偿,减少实际铣削误差[96]。
在多机器人参与的加工过程中,工件形貌、工艺参数、工作条件等带来多重限制,多机器人的末端路径、机器人本体均需要满足面向任务的时空约束。各个机器人应在指定时刻分别到达规划位姿,不能出现互相干涉,可采取分析协作过程中多机器人运动学/动力学约束关系的方法进行处理。多机器人协同系统具有封闭多回路、冗余驱动的特性,难点在于动力学建模、载荷分配策略,主流思路是建立优化判据并进行动载荷的最优分配。例如,利用双机器人的冗余特性,根据最小作用力原则优化多机器人的多位置抓持力分布[97];建立多节点闭运动链协调系统,引入线性加权方法约束多机器人的内部作用力,给出基于载荷分配原则的机器人协作吊运方案[98]。需要指出的是,机器人制造系统精度保障机制研究仍然停留在单机器人、单一工艺层面,而机器人协同加工的精度保障原理与体系层面研究仍处于空白阶段,后续需要攻关面向加工制造的机器人系统协同精度控制技术。
2. 机器人柔顺控制
机器人作业任务要求机器人末端与工件存在物理接触,对机器人与环境之间的接触力精度控制提出了较高要求。机器人末端微小的位置偏差都可能因被接触材料的形变而产生较大的接触力,或对机器人和被接触物造成损伤,需要在执行接触任务的机器人控制系统中添加力控制单元[99]。力位混合控制[100]、阻抗控制[101]在环境 – 机器人交互控制方面应用较多:相较前者,后者无需在两个正交方向分解出两套控制策略,鲁棒性更佳,机器人可稳定输出所需的作用力。早期研究关注机器人动力学的不确定性处理,多采用自适应阻抗控制方式,但阻抗控制模型结构相对固化而无法应对复杂的机器人工作环境。为此,引入考虑环境动态约束的机器人模型、受环境影响的可变控制模型,获得了更好的控制性能[102~104]。
随着机器人视觉技术的不断发展,视觉 / 力觉混合策略相较纯力觉控制方案纳入更全面的机器人作业信息,作业柔顺性更好。自然的做法是视觉/力觉信息独立处理,采用视觉比例控制、力觉比例积分控制策略,联合进行机器人关节角度控制[105]。也可采用视觉/力觉正交控制思路来简化控制策略,根据约束表面的几何信息预测视觉位移和接触力,将混合任务空间划分为正交的力觉控制子空间、视觉位控子空间,再由力觉、视觉分别控制不同的运动方向[106]。
在工业制造的实际环境中,环境模型的参数变化频繁,亟需一种泛用性和效率均较高的环境 – 机器人动力学建模方式,以确保机器人作业过程的末端跟踪质量。机器人加工属于具有强交互力的作业场景,需要控制系统及时捕捉接触力的变化并针对性调整控制策略。然而,机器人多传感器数据融合方法的计算成本较高,导致控制系统难以及时响应加工接触力的突变。为此,在多传感器数据融合方面需克服各控制子集的缺点,提高机器人对位置、接触力等物理量的测量精度以及多源数据处理的效率。
(四) 灵巧机构
在精密工业制造场景中,传统的机械抓手等机器人末端执行器,刚性结构的可形变范围小、关节运动自由度低、适应性不强、多关节柔顺性差,无法对不同尺寸、刚度、形状、类型的目标物进行高效率抓取及搬运。尽管已有机器人配置弹性材料并根据抓手模型设计自适应抓取策略,但无法根本性地解决相关问题。
由柔性材料制作的柔性抓手,可在无限的自由度上产生形变,利于模仿人的手部弯曲动作,自适应抓取刚度脆弱、结构复杂、尺寸多样的工业零部件[107,108]。例如,拉线抓手模仿肌肉收缩模式,可通过外部动力使抓手产生形变,但拉线需要预先嵌入抓手,拉线的线路和点位相对固定[109,110],导致夹爪行程有限,很难抓取形状不规则、质量较大的目标物体;为提高抓取效率,拉线抓手与黏性吸附、真空吸附等物理手段结合,进一步增强抓取动作的稳定性[111]。
得益于增材制造技术的发展,气动抓手因较低的制备门槛、材料具有弹性结构的特点而受到关注,多由纤维增强橡胶制成,经气压驱动形成俯仰、偏转、拉伸等自由度;还可进一步组合出多节点机构,执行灵活的动作任务[112]。传统的柔性抓手气动结构简单,但抓手刚度、承载能力较弱,因而目前多采用复杂气动网络结构[113]以增强抓手的性能;可根据任务类型灵活选择气动网络结构,在抓手的不同位置配置变形性能差异化的结构,兼具物品抓取、振动控制能力[114],从而在灵活性、刚度、承载能力之间取得平衡。此外,根据材料受激形变特性设计柔性抓手,如利用导电聚合物(EAP)材料在电压下产生变形的特性,设计特殊的EAP材料结构、电压驱动控制策略,即可控制抓手的抓取动作[115]。EAP柔性抓手具有较大的形变和输出力,可根据零部件的外形轮廓进行自适应调整,实现对目标物的稳定抓取;但EAP材料的机械强度很小,抓取时易受干扰[116],无法稳定抓取大尺寸目标物,也不宜用于多级协同任务。
四、 智能制造工业机器人技术发展趋势
(一) 大范围动态场景理解
工业机器人对环境、运行状态的感知要求极高,而在自主制造场景中作业环境多变、状态难以预估。需要构建动态语义地图以促进环境理解,解决机器人精细化实时路径规划、协同作业控制等难题;也需实时感知机器人与工件的关键信息,支持对制造状态进行全面监控。长久以来,大型部件制造过程中的信息感知环节普遍存在人工参与的现象,尽管多机器人视觉感知系统已投入应用,但并未显著缓解人为干涉多、自主性程度低、协同机制弱的情况。面向大型复杂部件制造的多机器人智能感知与认知研究仅处于起步阶段,由机器人实时环境感知、多源传感器自主测量与目标检测等构成的多模态感知理论体系亟待完善。针对复杂工业动态场景的大范围场景感知与理解,是未来智能制造工业机器人发展的重要方向。
(二) 集群化作业
智能制造的关键特征是机器设备之间互联、互通、互融,集群机器人协同作业则为高效协同、自主组织、增强学习、深度融合的智能制造理论与技术提供了关键能力支撑。集群机器人系统由一定规模的单体机器人组成,基于信息交互与反馈、激励与响应等交感行为,构建机器人之间的行为协同与自主决策能力,更好适应工业制造环境中动态变化的复杂作业任务。相较单体机器人,集群机器人系统的显著优势表现在:重塑大型复杂构件的测量、加工、装配等关键制造过程,执行单体机器人难以完成的制造与检测任务,对提质、增效、降本、柔性生产等发挥支撑作用。智能化的集群机器人制造是承担重大装备制造任务的有效形式、智能制造发展的重要趋势。
(三) 柔性作业
就目前广泛应用的工业机器人而言,机器人作业调试阶段仍大量采用人工示教方式(技术人员预先调试,设置机器人的动作路径)。而高端装备的各类关键核心部件,多有结构异形复杂、加工质量要求高、制造批量小、型号种类多的特点,导致机器人定制化作业调试模式难以胜任。智能制造工业机器人作为高柔性的智能制造装备,更好适应小批量、多品种、个性化的现代制造业生产模式,直接增强制造生产线的智能性和灵活性。为了高质量地执行焊铆、磨抛、装配、搬运等接触型作业任务,机器人需要准确跟踪预先轨迹,机器人的末端执行器与作业工件之间的位姿和接触力控制也显关键。对于接触型作业,人工操作在智慧性、灵巧性、柔顺性方面具有明显的优点,因而工业机器人在保持一致性、精准性、长时间连续作业等强项的同时,也需着力增强柔性作业能力。结合机器人作业特点,配置功能增强型传感器和末端执行器,提升机器人在接触过程中的操控性能,是实现人类技能与机器人作业模式融合互补的有效技术路径、智能制造工业机器人技术的重要发展方向。
(四) 具身智能
当前的工业制造模式由流水线定制化作业转向小批量、多品种的柔性离散作业,在制造场景、制造环境边界、制造任务三方面均存在不确定性。常规工业机器人的感知与作业能力有限,难以适应更趋复杂的工业制造环境。具身智能作为AI技术发展的重要分支,成为工业机器人的新兴研究方向,在工业制造中展现出良好潜力。具身智能机器人指具有具身智能能力的机器人,可理解人类自然语言感知环境,自主规划任务并与环境交互;突出机器人与环境的强关联、强交互,将更好应对柔性离散的工业制造环境。相关技术主要涉及多模态和泛传感的感知系统、精密运动控制系统、基于大模型技术与海量工业数据的世界模型,作为机器人与制造环境柔性适配的重要支撑,在智能制造技术体系中的地位不断提升。
(五) 网络化协同
工业机器人系统宏观有序地执行智能制造作业,需要以机器人个体之间的通信与计算为支撑。云计算、边缘计算、工业互联网、大数据等信息技术发展迅速,相关部署架构及应用平台集成了异构信息互通与计算力分配功能,可克服单个设备在传感、通信、信息存储、计算资源等方面的固有局限,是解决机器人通信计算融合问题的有力依托(见图3)。“云边融合”的工业机器人作业模式,全面集成振动、视觉、激光、电信号等传感器信息,深度感知制造过程中生产实体的特性与状态,根据作业任务属性、设备种类、计算性能,实时动态地在工业计算中心(云)和计算单元(边)之间进行数据交换、计算分配、任务分发,进一步延伸至场景中的智能制造设备;驱动机器人与其他制造设备高效、无缝地分配并共享云端即边缘端的计算、存储、数据资源,支持制造系统的网络化、智能化、多设备协同。基于云计算、边缘计算、云机器人等技术,构建高效安全的集群机器人通信计算一体化网络架构,保障机器人之间低时延、高安全的网络传输及计算分配,是未来智能制造工业机器人技术发展的另一重点方向。
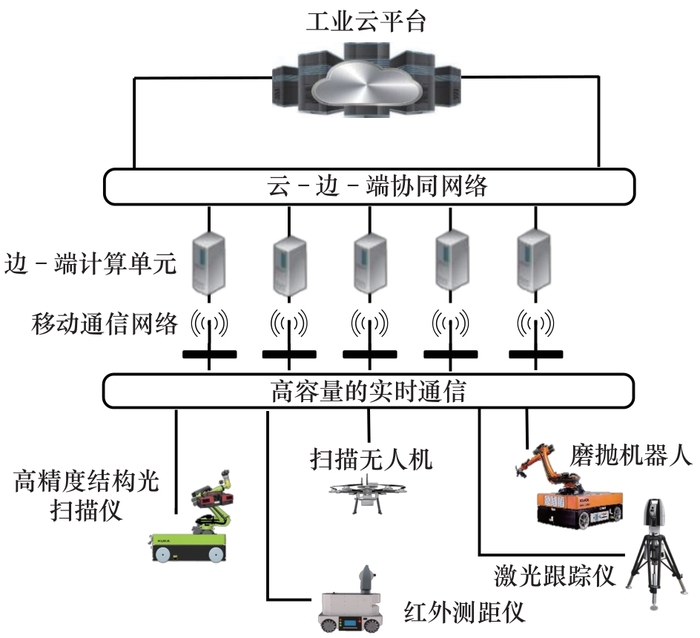
图3 云 – 边 – 端协同的智能制造集群机器人作业架构
(六) 数字孪生
数字孪生以数字化方式创建制造场景、设备、零部件等实体的虚拟模型,可模拟物理实体在现实环境交互中产生的外观行为、内在物理特性变化。对于智能制造工业机器人,基于数字孪生技术开展虚实交互仿真、虚实映射反馈、数据融合分析、预测迭代优化,增强或扩展机器人制造系统的功能,监控机器人系统的运行情况,预测并优化机器人作业参数,将显著增强复杂力、光交互环境中的作业性能(见图4)。相关系统已在多类装备制造领域开展应用,如基于数字孪生技术的飞机智能制造平台,将飞机实际生产数据融入到飞机制造数字孪生系统,建立飞机制造场景孪生模型,与制造执行、任务规划系统连通,提前规划制造任务,支持快速调整制造参数。然而,机器人与制造环境复杂交互的数字孪生仍存在不足,数字孪生建模精度不高,机器人多传感器数据交互整合困难,数字孪生预测的准确性和实时性欠佳;需要着力开展相关技术攻关,才能稳健推动智能制造工业机器人数字孪生技术的发展与应用。
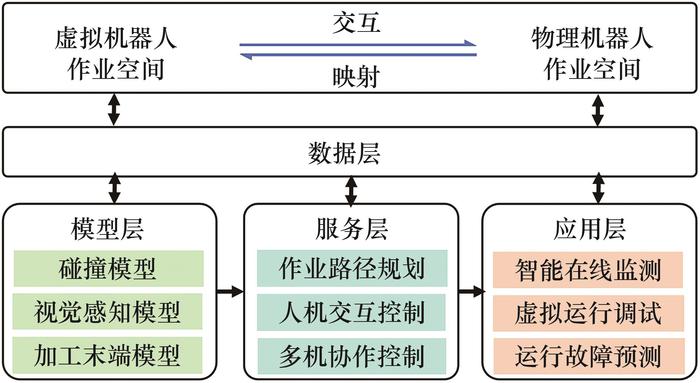
图4 工业机器人数字孪生系统
五、 结语
本文围绕智能制造工业机器人作业这一主旨,梳理了智能制造工业机器人的应用背景和作业类型,总结了在航空航天装备、海洋船舶、轨道交通装备、新能源汽车、电子信息产品等代表性制造领域的应用情况,从视觉感知、决策规划、运动控制、灵巧机构等方面综述了相关共性技术的研究进展。在前瞻相关技术发展趋势的基础上认为,智能制造工业机器人技术的全面突破,将提升我国制造业的生产效率、技术水平、产品质量,为我国制造业高质量发展开辟新途径。
工业制品市场需求变化迅速,先进制造技术也在快速迭代,小批量、多品种、柔性化、易部署的多机器人智能制造系统将成为发展主流,多机交互、人机交互、机器人与场景交互的广度和深度也将不断拓展。为应对复杂的交互需求,智能制造工业机器人技术需要在动态场景理解、集群化作业、柔性作业、具身智能、网络化协同、数字孪生等方向着力突破,探索构建感知 – 规划 – 控制一体化的复杂多维协同作业机制。加快形成制造模式柔性化、制造过程信息化、制造工序无人化的新型生产方式,为化解高端装备制造难题提供新型解决方案,支撑高端装备制造业的数字化、网络化、智能化转型升级。
来源:中国工程科学
作者:吴昊天、王耀南、朴玄斌、陈文锐、江一鸣、贾林、肖旭、彭伟星